One of a small team of independent consultants that assisted Valent BioSciences (VBC) in working with their architects and engineers to develop the design of a new 80,000 SF Biorational Research Center containing laboratories, greenhouses and supporting facilities for development of biorational pesticides. Assisted client with value engineering to bring the design in line with the project budget. Prepared design requirements specification for compliance with the United States Department of Agriculture (USDA), Animal and Plant Health Inspection Service (APHIS), Plant Protection and Quarantine (PPQ) requirements for containment of plant pathogens and pests. Coordinated the design of the greenhouses and headhouse with users, architects, engineers and the greenhouse manufacturer. Reviewed and commented on design documents, including fermentation and downstream processing laboratory and pilot plant areas.
Company: Valent BioSciences LLC |
Location: Libertyville, Illinois |
Total installed cost: $28 million |
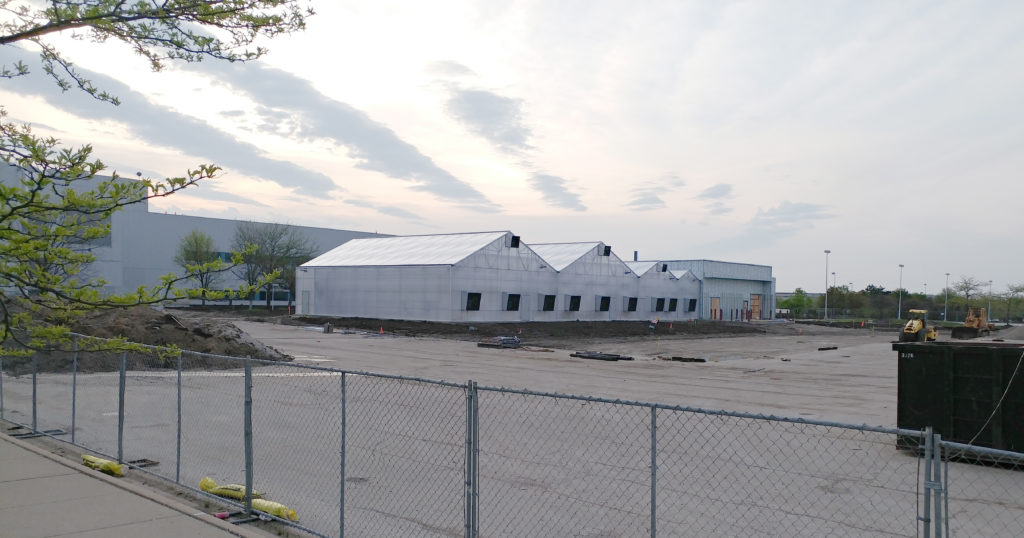
Contents
Project Overview
The VBC Biorational Research Center opened in 2018 in Libertyville, Illinois in a building near the VBC corporate headquarters. The building was originally a Motorola factory that was converted into a stylish multi-tenant workplace called Innovation Park. The VBC portion consisted of 67,000 SF of research laboratories and supporting facilities in the remodeled existing buildings and 8,500 SF of new gutter-connected greenhouses with a 4,000 SF attached headhouse connected to the existing buildings. The facility includes chemistry, plant pathology, nematology and entomology laboratories, plant growth chambers, an insectary, a microbiology suite, fermentation and downstream processing pilot plants, and a formulations suite and pilot plant. All of this replaced their previous facilities that were located on a nearby historic farm, where many of the laboratories were in old converted barns and chicken coops.
Design Involvement
VBC asked me to join the project as they thought they were completing the Schematic Design phase of the project. However, as is often the case, the design did not match the budget and considerable rework of both the design and the budget occurred before the two were aligned. In addition, the project scope was not yet fully defined. I assisted VBC with filling in the blanks to define the project requirements, particularly in the areas of APHIS PPQ containment requirements and developing the greenhouse and headhouse design as described below. Greenhouses consume substantially more utilities than most laboratories and I compiled estimates of utility requirements for the greenhouses. I also coordinated development of the total utility requirements for the project to assure that utility supplies and piping were sized correctly.
I also reviewed and commented on the design of the rest of the facility. In particular, I focused on the fermentation and downstream processing pilot plants as I have an extensive background in fermentation process development. My involvement continued through Design Development, selection of the general contractor, and preparation and finalization of the Construction Documents.
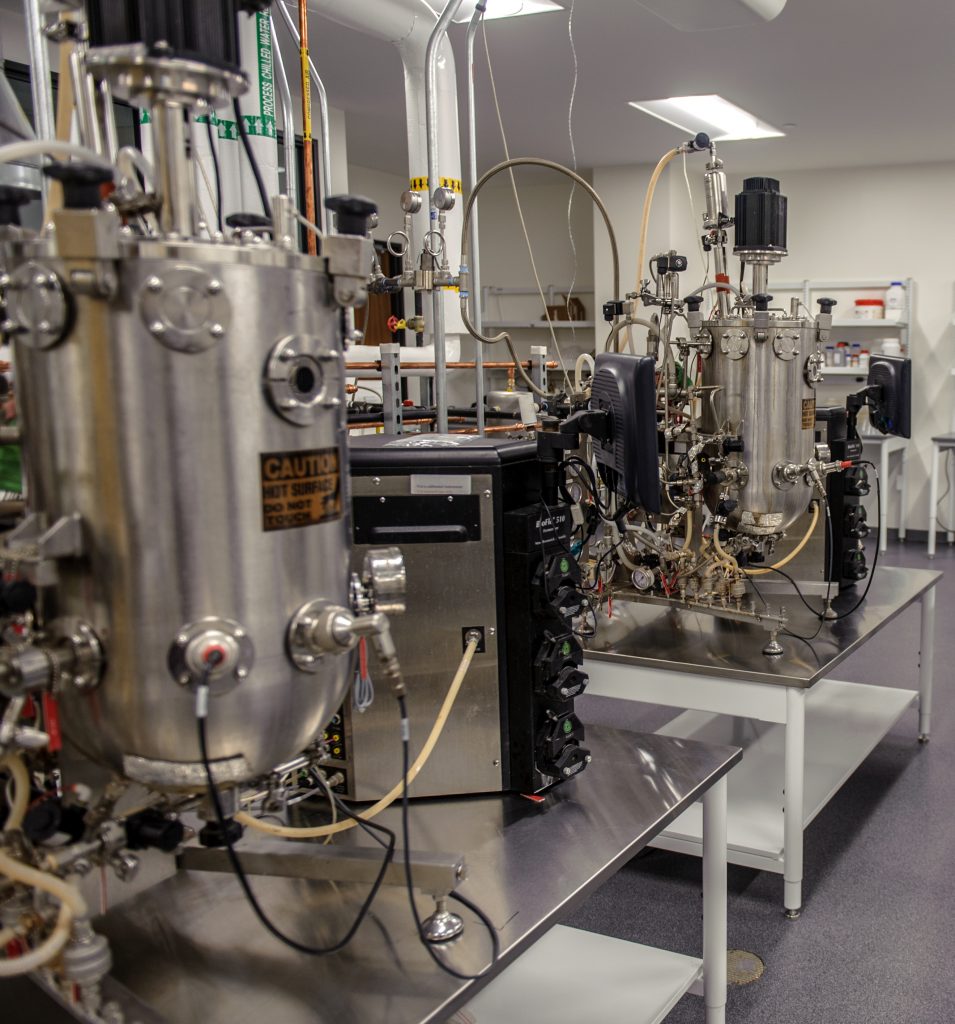
APHIS PPQ and Recombinant DNA Containment Requirements
The USDA regulates the use of non-indigenous plant pests and pathogens through its Animal and Plant Health Inspection Service (APHIS), Plant Protection and Quarantine (PPQ) program. Nearly 40 rooms or other spaces in the Biorational Research Center were designated plant pest or pathogen containment areas that required special architectural and engineering design features to prevent the release of these organisms into the environment. In addition, VBC wanted the option of being able to work with recombinant microorganisms in the future. I assisted VBC by cataloging these spaces and preparing a specification for the exact design requirements of each space based on a set of PPQ containment guidelines and the NIH Guidelines for Research Involving Recombinant or Synthetic Nucleic Acid Molecules. This specification became the basis for the design development and their permit application, allowing them to seamlessly transfer their research cultures from their previous facilities to the new research center.
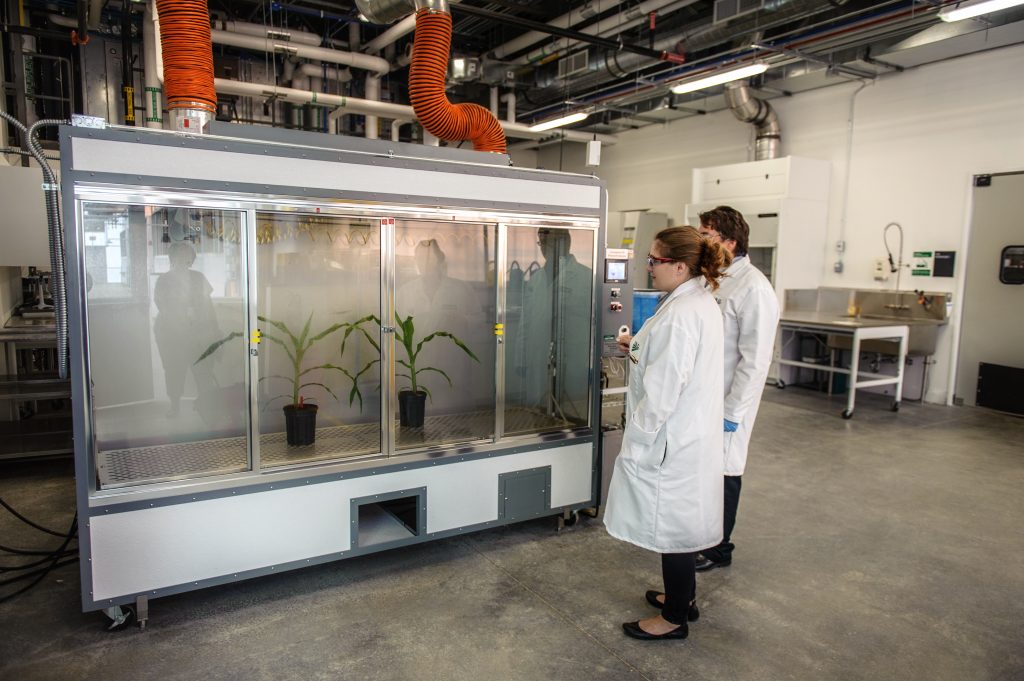
Greenhouse & Headhouse Design Coordination
On this project, VBC decided to manage the design, procurement and installation of the greenhouses and the greenhouse equipment themselves. However, the architects and engineers were still responsible for the design of the entire headhouse, the greenhouse foundation and the mechanical, electrical and plumbing connections to the greenhouse equipment. All of this required considerable coordination of the design between the architects, engineers, greenhouse supplier, and the greenhouse heating, irrigation and controls systems suppliers. I provided this coordination through the review and redlining of each suppliers’ design package and the facilitation of design review meetings between the various parties.
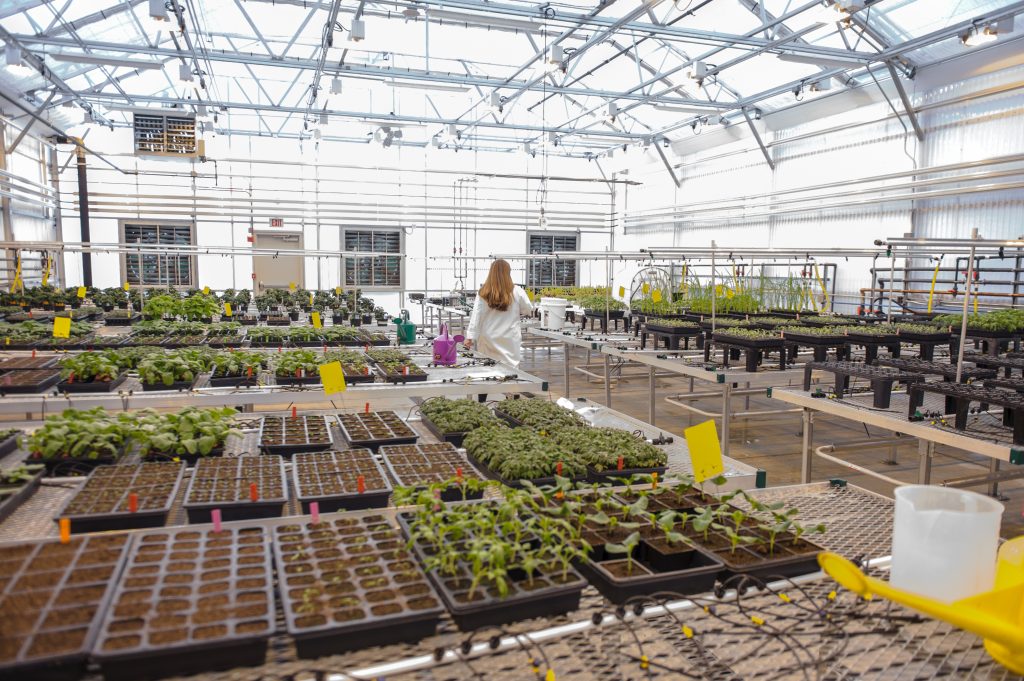
I also used my horticulture background to facilitate an agreement on the design of the landscaping around the greenhouses to meet the village building codes and the landlord’s requirements for screening the structures without blocking too much of the natural light to the greenhouses. For anyone thinking of building a similar project, this is an important lesson: Don’t assume that your landlord understands that greenhouses need the maximum amount of natural light. The time to reach this understanding is when you are negotiating the lease, not after you already signed it and are trying to get the “issued for construction” drawings to the contractor.
Greenhouse Automation
VBC selected an Argus Control Systems Ltd. control system for the greenhouses which controls the heating, cooling, ventilation, irrigation and supplemental lighting and carbon dioxide systems. As with the other greenhouse systems, the design of this system required considerable coordination between Argus, the greenhouse equipment suppliers and the project electrical and mechanical engineers. My design coordination role included reviewing and commenting on the design packages from the various suppliers and developing a detailed system integration plan for how the Argus control system would work with the Building Automation System (BAS) that controls the rest of the laboratory complex.
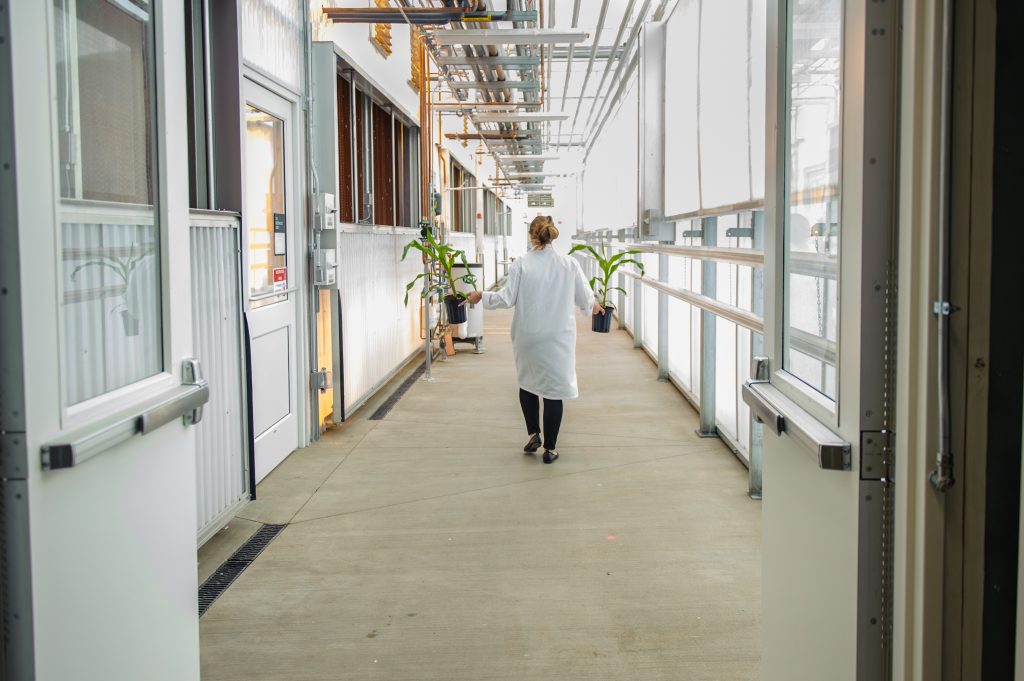