I have been involved in the development of manufacturing process automation for over twenty-five years. I come from the first generation to have computers in high school, in our case, the computer was an 8k Wang that recorded programs on a cassette tape. We used to go through our lines of code and take out spaces just so we could add another line of code. I’m also old enough to have written some programs on punched cards when I took classes in programming at a local college while still in high school. I still remember the keypunch machines stacked in the hallways of the computer department when the first CRT terminals replaced them.
Contents
Experience
My first hands-on process automation experience was during development of a meta-hydroxyphenylacetylene biotransformation process while at Bio-Technical Resources. When I joined Novo Nordisk, my proficiency in BASIC meant that I quickly became the maintainer of the old Foxboro FOX 3 process computer that was running three of our fermentors. I joined Novo Nordisk just prior to a major plant expansion and worked closely with the automation team to develop and test the new SattLine Distributed Control System (DCS) batch process control software for the new fermentation building. This was around the time the ISA-88 batch processing standard was being developed and first released and we were adapting continuous process control systems to a batch environment.
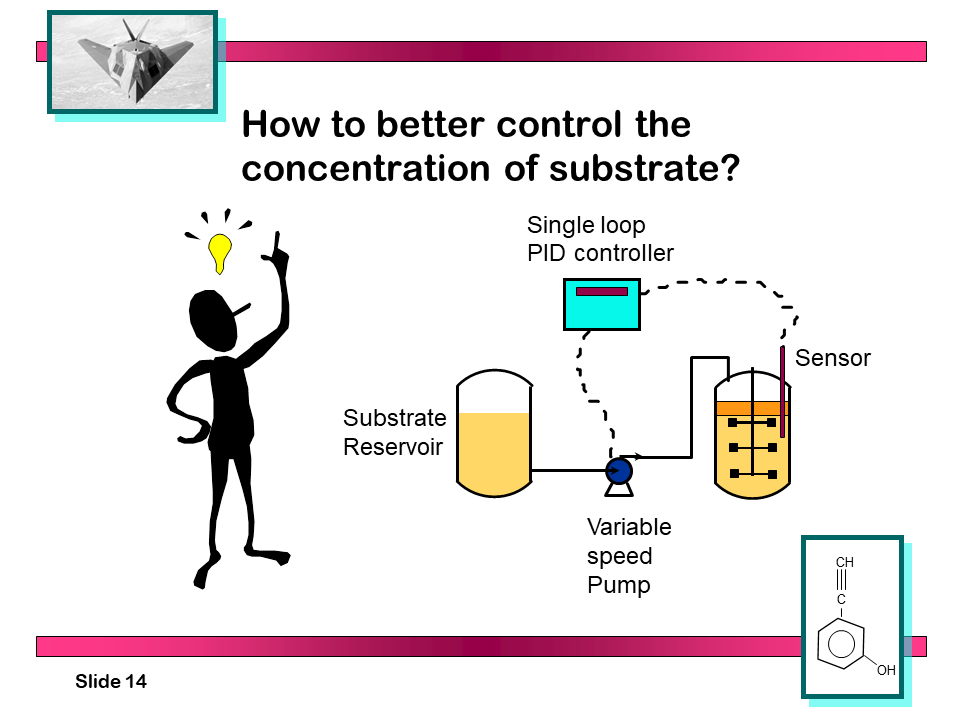
More recently, I was closely involved with the development of the Emerson DeltaV DCS controls logic for the Valent BioSciences greenfield biopesticides plant. It was refreshing to see how far implementation of the ISA-88 batch standard had come in the DCS world. Working as a consultant to Valent BioSciences, I was part of the team that evaluated the DCS vendor bids and selected Emerson and DeltaV for the project.
Prior to the startup of their Osage, Iowa plant, Valent BioSciences had toll manufactured their products at the Abbott Laboratories plant in North Chicago. Using the Abbott manufacturing directions, the new plant design documents and the Abbott PROVOX DCS source code as a basis, I wrote all of the fermentation area functional control specifications (FCSs) for the plant. I also reviewed and commented on the FCSs for the utilities, raw materials and downstream processing areas. I reviewed and extensively commented on the documentation developed by Emerson for the fermentation area programming and participated in portions of the factory acceptance testing. As some skid-mounted systems were procured with their own PLCs, part of my responsibilities included performing a systems integration role by coordinating the design of the PLC logic with the DCS logic. In some areas, this coordination role continued into plant startup, working with both the Emerson DCS automation team and third-party PLC programmers.
The process simulation modeling software that I use to assist my clients with development of new or modified processes is specifically designed for batch processing and uses the same process model structure as ISA-88. This greatly facilitates translating a simulation model into both a physical process and a process control strategy.
The following is a list of my projects that have included significant automation development work.