Consultant/Lead Process Engineer for preliminary and detailed design of $150 million greenfield biopesticides fermentation plant in Iowa. Developed block flow and process flow diagrams and process design basis. Reviewed and provided comments on material & energy balance, P&IDs, piping specifications, equipment specifications, instrument specifications, shop drawings, and 3-dimensional equipment and piping models. Actively involved in selection of distributed control system vendor and development of plant process control systems. Recommended cost savings and process improvement opportunities.
Unit operations: Fermentation, Sterile nutrient dosing, Rotary separation, Vibratory separation, Basket centrifugation, Disc stack separation (centrifugation), Ceramic microfiltration, Filtration (belt, filter press), Distillation (solvent recovery), Thin film evaporation, Forced circulation evaporation, Ion exchange separation, Reverse osmosis filtration, Liquid–liquid extraction (Podbielniak centrifugal extractor), Crystallization, Vacuum drying (helical dryer), Continuous media sterilization, Pneumatic conveying, Tank truck unloading and loading |
Products: Bacillus thuringiensis (Bt) biopesticides, Bacillus (Lysinibacillus) sphaericus biopesticides, Myrothecium verrucaria biopesticides, Aminoethoxyvinylglycine (AVG) from Streptomyces sp. fermentation, Gibberellic acid (GA3) from Gibberella fujikuroi fermentation, Gibberellins A4+A7 (GA4A7) from G. fujikuroi fermentation |
Company: Valent BioSciences Corporation |
Location: Osage, Iowa |
Total installed cost: $150 million |
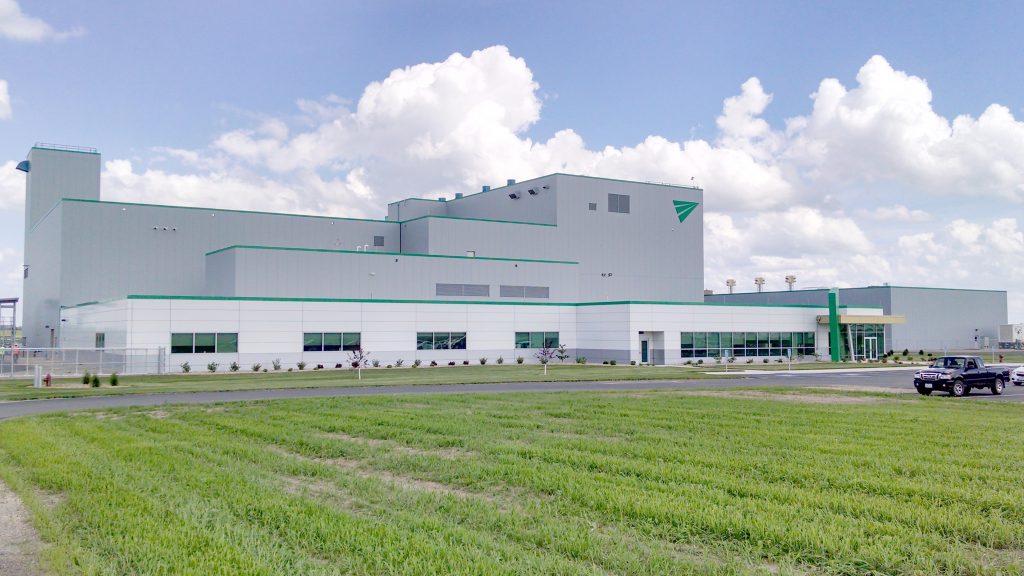
“Middough’s mad scientist was way better than the other engineering companies’ mad scientists”. That statement from one of the Valent BioSciences Corporation (VBC) managers was how I began my work with VBC. At the time, I was a project engineer working out of the Middough engineering offices in the Chicago area. Middough had been invited to bid on the engineering design of this new plant and I was the process engineer member of the sales team that presented Middough’s qualifications to VBC. Middough won the contract, and I like to think I helped clinch the deal by mentioning to one of the VBC managers that I had read a book on gibberellins1 as we left the meeting.
Contents
Preliminary Engineering
While at Middough, I was the lead process engineer for the preliminary design and cost estimate of the plant and drew some of the first block flow diagrams of the VBC fermentation and downstream processing operations. I also developed the first draft of the design basis. At the time, the VBC products were toll manufactured by Abbott Laboratories in North Chicago. As our starting point for the design, we were handed stacks of Abbott manufacturing directions, bills of materials, P&IDs, equipment specifications and drawings, and a few PowerPoint presentations with high-level process overviews. The Middough process engineering team had to sift through all of this information to extract the actual manufacturing processes and develop the preliminary design.
Detailed Engineering
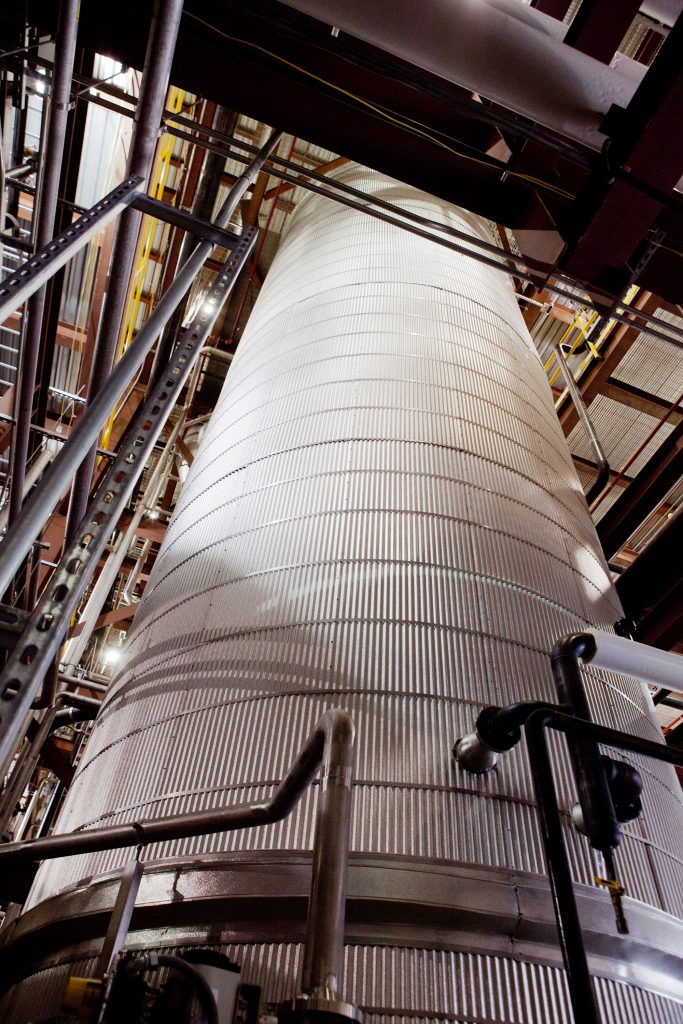
After I left Middough, VBC hired me as a direct consultant on the project. As VBC had only a small engineering group and no plant design experience, I effectively became their lead process engineer. I was actively involved in all aspects of the detailed engineering design, including reviewing and commenting on the various discipline design bases, P&IDs, piping specifications and equipment specifications. As the Middough team had limited experience with sanitary design for industrial fermentation plants, I spent considerable time developing the sanitary piping and instrument specification details.
I also participated in the endless 3-D model reviews where we walked down every sanitary line to assure that it had no dead legs and the steam and drain lines were properly located for both sterilization and operator access. I was also an active participant in the detailed process hazards analysis.
Process Automation
Having a modern process automation system was important to VBC management and the detailed engineering design included preparation of a specification for the plant distributed control system (DCS). I worked with the Middough instrument and controls engineers to develop this specification and a set of critical functional requirements to objectively score the DCS candidates. Five DCS suppliers were invited to present their products to a group of Middough and VBC evaluators and from these, VBC selected the Emerson DeltaV DCS.
The VBC project staff and I developed most of the detailed functional control specifications (FCSs) for the plant. Using the Abbott manufacturing directions, the new plant design documents and the Abbott PROVOX DCS source code as a basis, I wrote all of the fermentation area FCSs for the plant. I also reviewed and commented on the FCSs for the utilities, raw materials and downstream processing areas. I reviewed and extensively commented on the documentation developed by Emerson for the fermentation area programming and participated in portions of the factory acceptance testing. As some skid-mounted systems were procured with their own PLCs, part of my responsibilities included performing a systems integration role by coordinating the design of the PLC logic with the DCS logic. In some areas, this coordination role continued into plant startup, working with both the Emerson DCS automation team and third-party PLC programmers.
Epilogue
Following the startup of the Osage plant, I continued to consult for VBC and was a member of the project team for their next major capital project, the Biorational Research Center. I have also developed a set of process simulation models of the major Osage products to assist VBC with understanding their manufacturing costs and planning future plant expansions.
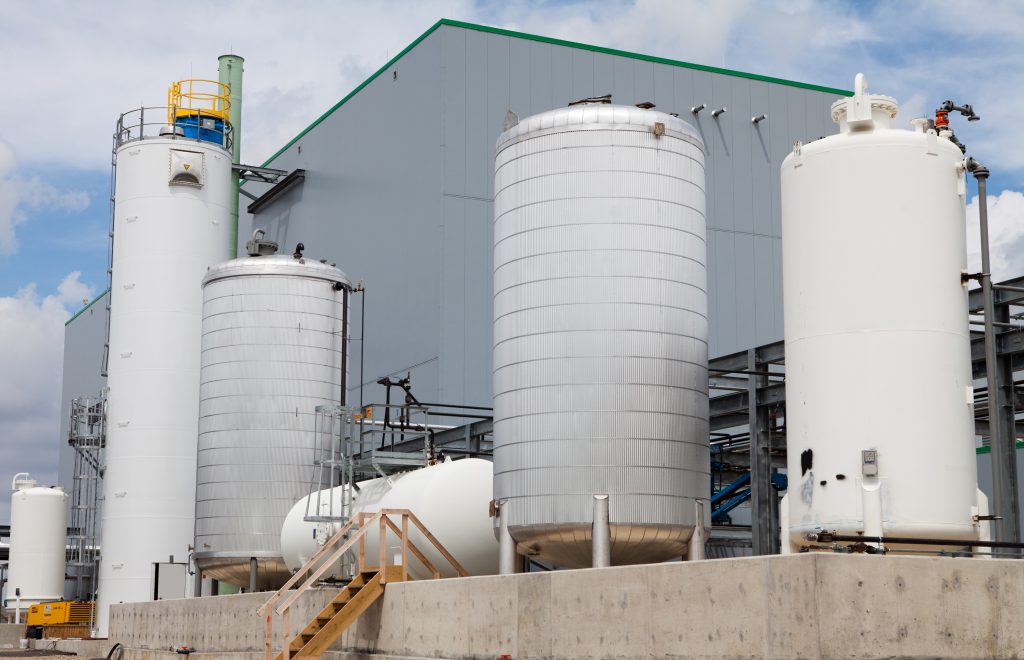
1 Crozier, A. (Ed.). (1983). The biochemistry and physiology of gibberellins. Praeger Publishers.